Production
Production
All our products benefit from high-quality production , carried out in the heart of the Plastics Valley , in Oyonnax . This territory is world-renowned for its expertise in plastics processing, thus guaranteeing the reliability and durability of each part we manufacture. Our production is based on local know-how that ensures exceptional quality standards.
How does our production work?
We use modern processes such as injection, extrusion and thermoforming. These techniques allow us to create articles that meet the specific requirements of our customers. By choosing premium materials and adopting advanced manufacturing methods, we are committed to meeting the highest standards in the industry. Our goal is to provide innovative products that combine performance and safety for all users.
Procedures
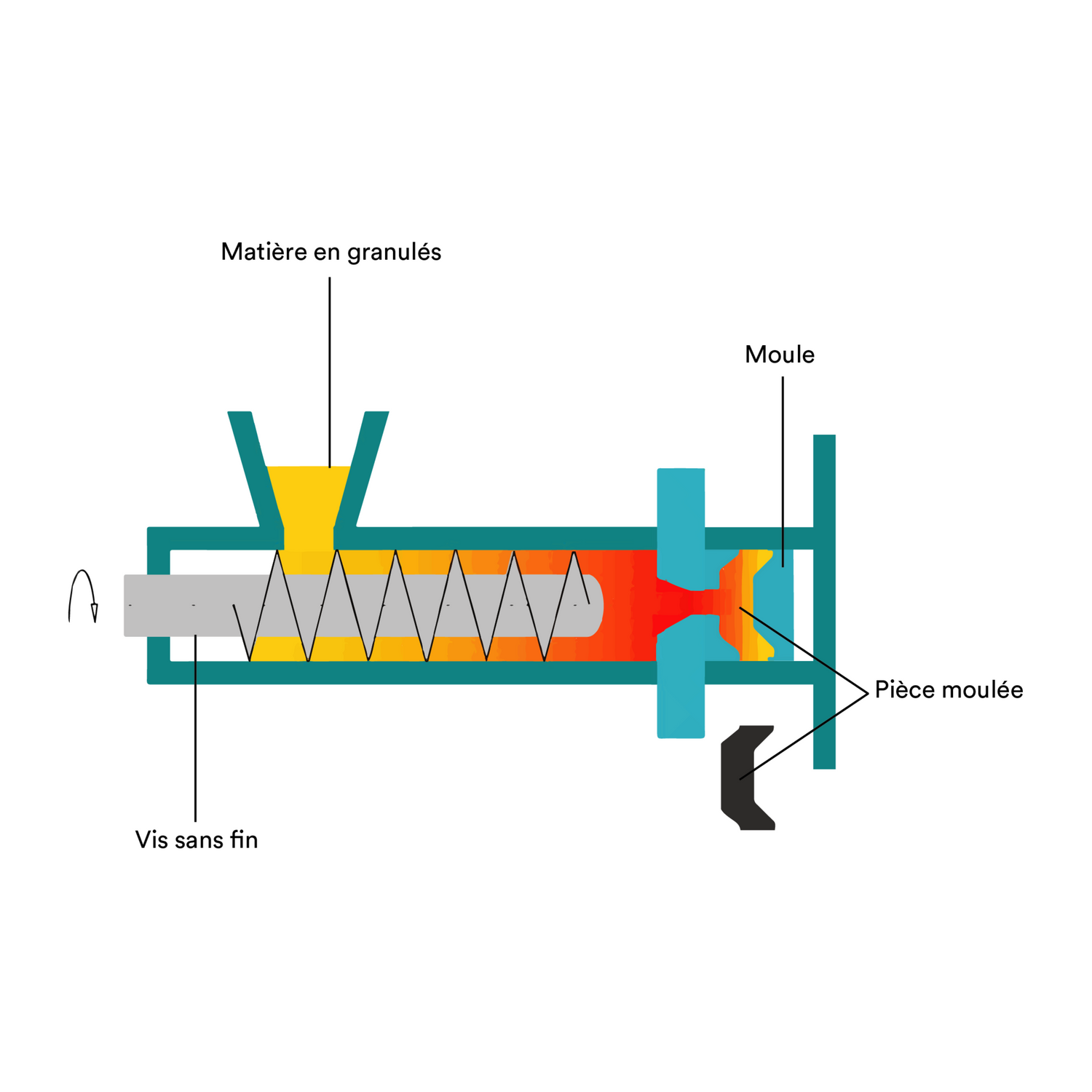
Injection molding
Injection molding is a key manufacturing process that produces plastic parts with high precision. The process involves heating plastic pellets until they melt, then injecting the liquid plastic into a mold under high pressure. Once cooled, the plastic hardens and takes the shape of the mold, ensuring strong, durable products that are suitable for a variety of uses.
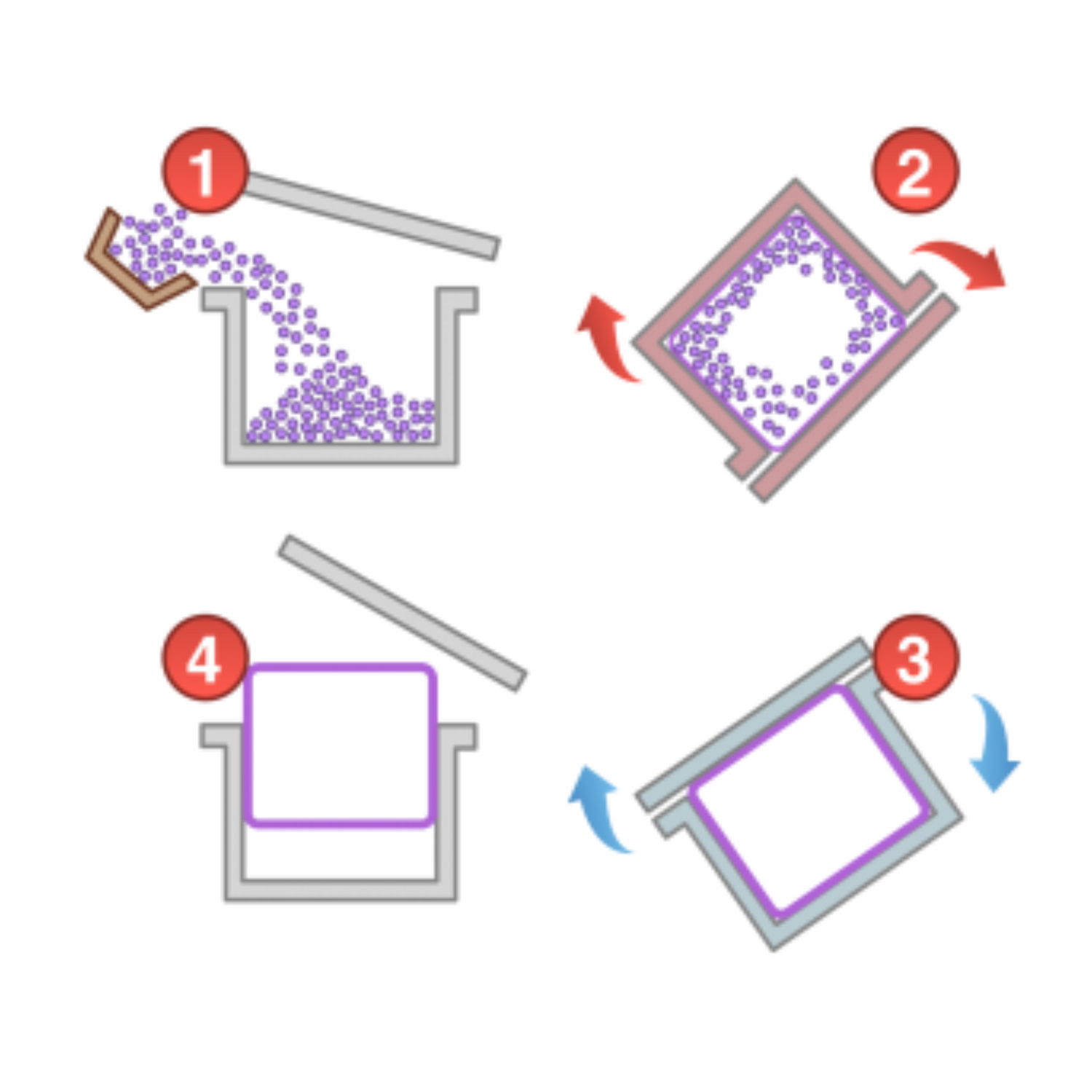
Rotational molding
Rotational molding is a manufacturing process that produces hollow , strong parts. First, plastic granules or powder are placed in a hollow mold. Then, the mold is closed and heated, allowing the plastic to melt. Once the plastic has melted, it spreads evenly over the inner walls of the mold and hardens to its final shape. Finally, the mold is opened to remove the part, which is solid and seamless . This process guarantees high strength and durability for complex shapes. Rotational molding is notably used to manufacture the Cub-Notti .
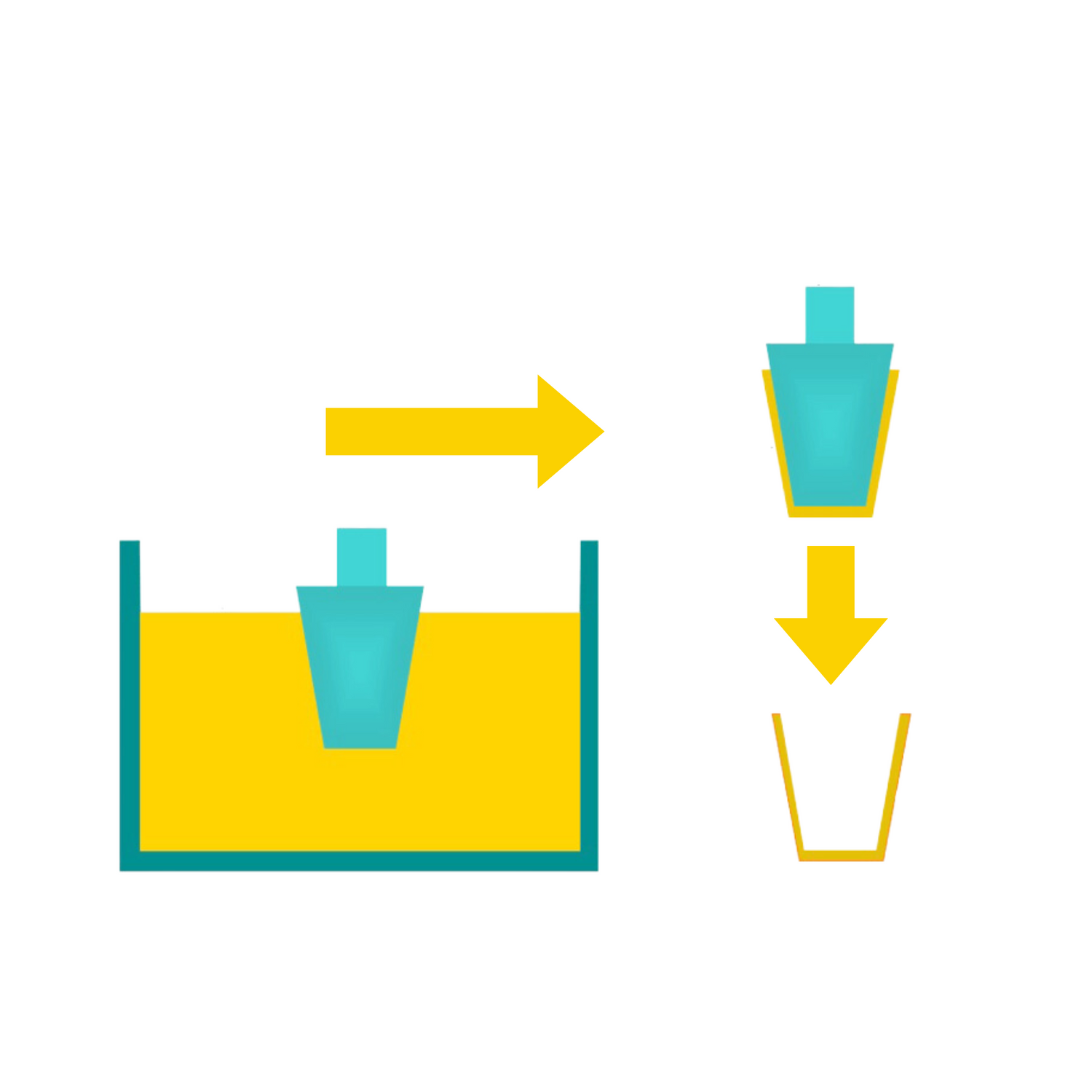
Plastic soaking
Dipping is a manufacturing process that creates strong plastic parts. It involves heating a silicone , then submerging a metal part into the hot silicone.
When the part is removed, a layer of silicone adheres to its surface, providing protection and flexibility. This process combines the strength of metal and the flexibility of silicone.
It is used for Cup-Notti , where an iron bar is twisted and then dipped in silicone, ensuring durability and aesthetics.
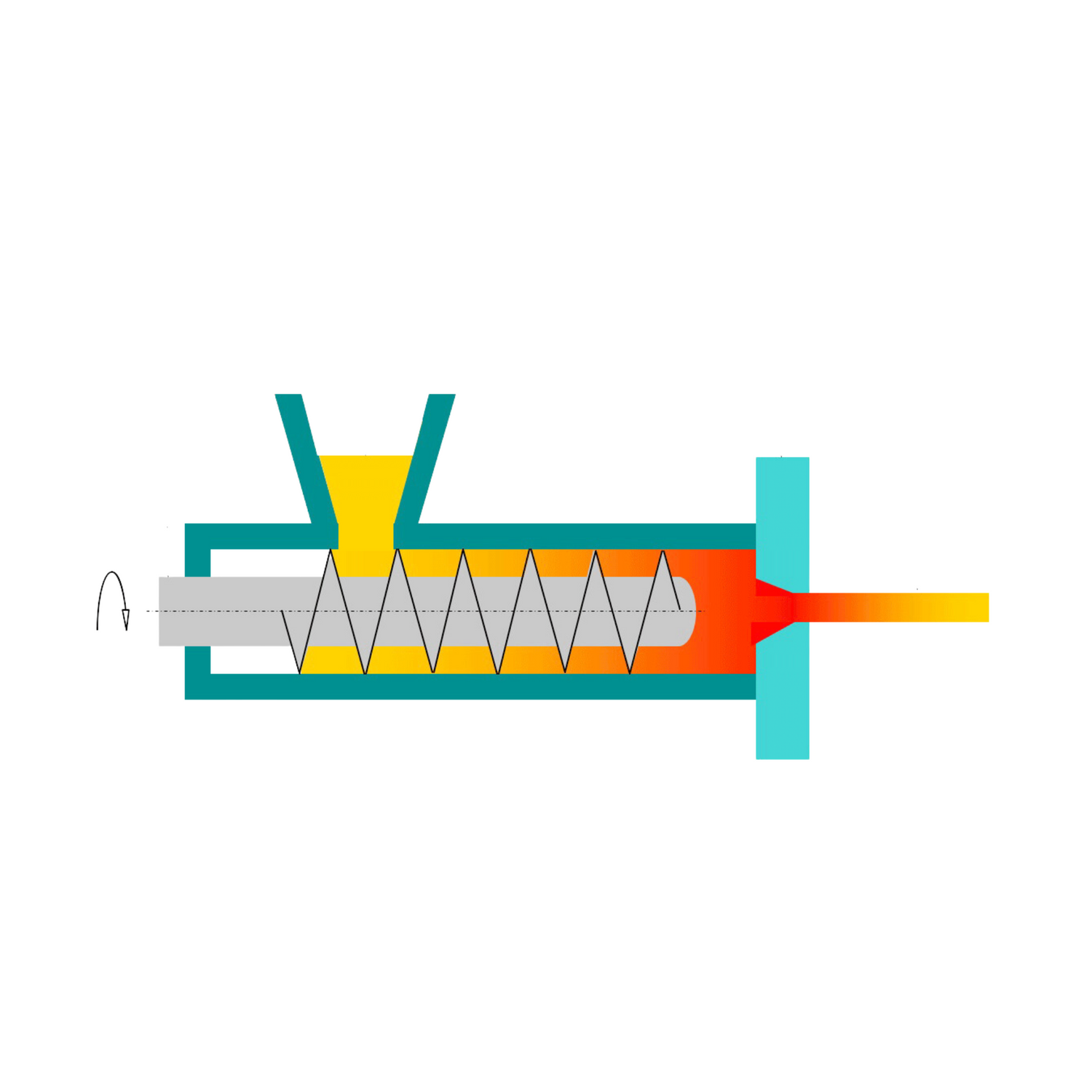
Extrusion
Extrusion is a manufacturing process that creates continuous parts, such as the Cup-Notti clamp . The process begins with the melting of plastic materials, which are then forced through a die to shape the product.
Once extruded, the parts are cooled, then twisted and cut to the desired length. This process allows for precise and uniform shapes, while ensuring good strength.
Extrusion is ideal for the manufacture of the Cup-Notti with clamp , offering both durability and performance in its use.